The pandemic highlights the value of HealthTrust’s efforts to stay vigilant
Drug supply threats aren’t new. But the COVID-19 pandemic has undeniably disrupted the supply chain in new ways, reinforcing the importance of HealthTrust’s efforts to mitigate drug shortages and create new inventory protections for members.
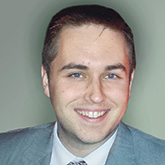
Greatly increased costs for raw ingredients, labor and shipping over the past two years—along with global manufacturing interruptions—have all contributed to the difficult landscape. “It feels like a bit of a perfect storm,” says Christopher Little, PharmD, Senior Director, Pharmacy Innovation, HealthTrust. “I think COVID has just exacerbated the challenges. It hasn’t created anything new, but it’s certainly shown us where the vulnerabilities are.”
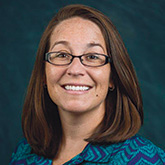
Indeed, the pandemic highlights just how dependent the U.S. has been on the international supply chain, agrees Christine Dunn, PharmD, AVP, Pharmacy Sourcing, HealthTrust. “But the pandemic made it worse, because globally, everyone was going through the same thing at the same time,” she says.
Front-line challenges
Inevitably, facilities have needed to purchase alternate products or ration others when certain go-to drugs and related supplies have been lacking in recent months. This includes sodium chloride solution, a mainstay product clinicians use to flush lines or reconstitute medications, according to Christopher French, PharmD, MBA, Director, Clinical Pharmacy Operations, HealthTrust. To adapt, he says, some hospitals have drawn small vials of sodium chloride from large-volume bags, creating the need for workers to use additional safety precautions.
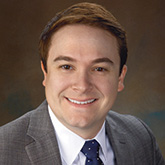
“It ends up resulting in a lot of work within a facility to continue providing safe care to patients,” Dunn shares. “And, it adds to the overall anxiety that staff are feeling, wondering: ‘Are we going to get product? If not, how are we going to take care of the patients?’ ”
Even the availability of the tiny glass vials that contain individual doses of medications has been vulnerable to COVID’s domino effects, as they’re needed in mass quantities for the vaccines. “Vaccine production is undoubtedly important, but it requires utilizing manufacturing lines that historically may have been used for other products,” French explains. “Either some products are not going to be manufactured for [several] months in favor of vaccines or COVID-related medications, or the production cadence is reduced, causing further product shortages.”
Well-established mitigation efforts
Long before the pandemic, HealthTrust established various programs and protections to mitigate drug supply disruptions. “We’re supporting our health systems with additional resources, so they don’t have to spend as much time navigating drug shortages in general,” French says. “They can spend more of their time devoted to patient care.”
These efforts include the SIMS (Supply Interruption and Mitigation Strategies) program, which involves maintaining a “living list” of products considered critical for members and strategizing with suppliers to ensure enough of these products is always on hand, Little says. “We refer to this as our ‘never-out’ list—products so important that we never want our members to be out of them,” he adds.
Fulfilling SIMS goals has required pushing manufacturers for greater transparency into their own supply chain hiccups, which had previously been an uphill battle. “We’re not just going to supplier partners and asking about price; we are also digging deep on redundancies and where they’re sourcing their raw materials from, so we can protect and diversify ourselves as much as possible,” Dunn explains. “We’re trying to understand their entire supply chain from raw material to finished product, so we can have a level of confidence.”
By strategically partnering with one of the largest pharmaceutical distributors, McKesson, HealthTrust also set up a unique control channel to secure additional segregated inventory of key products for members.
This alliance particularly paid off in 2020, when the sedative propofol was in otherwise short supply because of high demand for COVID-19 patients on ventilators, French adds.
“From a contracting perspective, there are a couple of protections we’ll now add for certain products,” Little explains. “We are now routinely asking manufacturers to sequester inventory for HealthTrust. Ultimately, we are reducing manufacturers’ risk by giving them a stronger commitment and reducing our risk by having product we can more readily plan on being available.”
New initiatives
Going forward, HealthTrust will include more of these secured inventory protections in agreements with suppliers, French says. Other ideas under consideration include closely monitoring major ups and downs in drug pricing and locking in low prices on certain medications when the market hits a low. “We’ve been trying to identify where we think those pricing floors could be getting close—even if those items are not at risk today—and adding some contractual securities to ensure volume and protections so our members have a reliable supplier,” Dunn explains.
Additionally, HealthTrust is combing through cumulative data to see signals of supply disruption and be more proactive. “Right now, they’re nascent efforts, but we’re utilizing technology to see if we can more quickly identify a potential supply disruption,” Dunn adds.
To maximize the benefits from these initiatives, HealthTrust members need to keep communication lines open. “We want and need member feedback to understand their challenges,” Little says. “If we know where they’re heavily impacted, it gives us ammunition to prioritize what product we go after next and allows us to contract better on their behalf.”
To share your feedback about drug supply challenges, email your Account Director. Read more about HealthTrust’s SIMS program.
Share Email COVID-19, Drugs, Q2 2022, SIMS